In today’s highly automated and data-driven industrial environments, fault detection and classification (FDC) Industry has become critical to ensuring quality, reliability, and uptime in manufacturing and production processes. As industries adopt smarter technologies, Artificial Intelligence (AI) is emerging as a transformative force in the FDC space—enhancing the speed, accuracy, and adaptability of fault management systems across sectors like semiconductors, automotive, electronics, energy, and more.
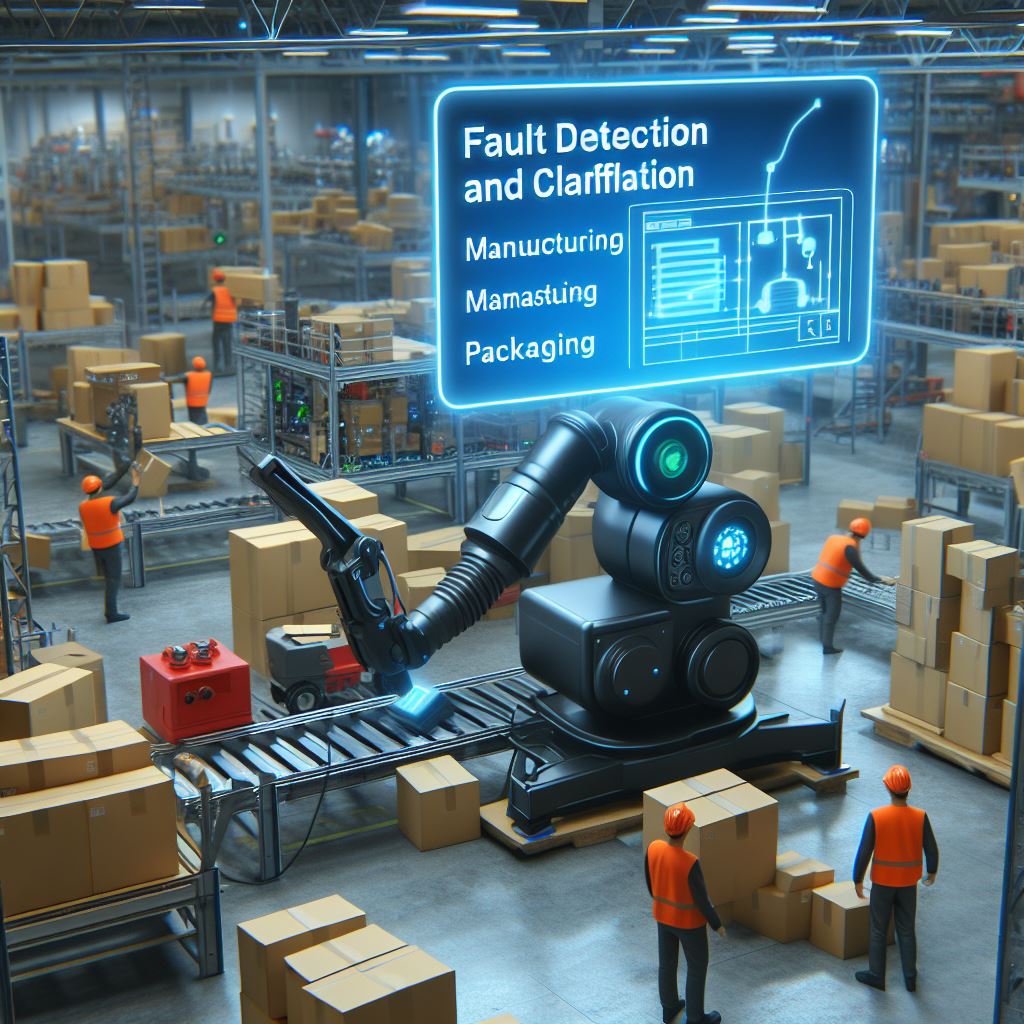
AI-driven FDC systems not only detect equipment anomalies or process deviations earlier but also offer automated root cause analysis, real-time classification, and predictive diagnostics, helping manufacturers move from reactive maintenance to truly proactive operations. This shift is reducing downtime, improving yield, and ultimately driving greater operational efficiency.
AI Enhances Accuracy and Speed of Fault Detection
Traditional FDC systems rely on static rules and threshold-based models, which are often prone to false positives or negatives and may not adapt well to new conditions. In contrast, AI-powered FDC platforms use machine learning (ML) and deep learning to analyze high-frequency, high-volume data from sensors, production tools, and control systems.
These algorithms learn complex patterns from historical and real-time datasets to identify subtle anomalies that signal early-stage faults—long before they impact product quality or cause system failures. AI can also correlate multiple parameters simultaneously (e.g., temperature, vibration, voltage, and flow), detecting faults that would otherwise go unnoticed using conventional monitoring systems.
Intelligent Classification and Root Cause Analysis
One of the most significant contributions of AI to FDC is in the classification and diagnosis of faults. Instead of simply flagging an anomaly, AI systems can classify faults by type (mechanical, electrical, process-related, etc.) and even pinpoint the most likely root cause using techniques like neural networks, decision trees, or natural language processing (NLP) for maintenance logs.
For instance, in semiconductor manufacturing—a sector where FDC is critical—AI can distinguish between tool-induced defects, process variations, and wafer contamination. This enables faster corrective actions, reduces scrap rates, and improves overall yield. AI can also continuously refine its classification models based on newly labeled fault data, becoming more accurate and adaptable over time.
Real-Time Monitoring and Predictive Maintenance
Modern production lines generate enormous volumes of time-series data that need to be monitored in real time. AI-powered FDC solutions leverage streaming analytics and edge computing to detect faults the moment they occur—or, in many cases, predict them ahead of time.
By analyzing trends and detecting early signs of equipment degradation, AI enables predictive maintenance strategies that reduce unplanned downtime and extend the lifespan of critical assets. Instead of following fixed maintenance schedules, organizations can service equipment just-in-time, saving both time and cost.
Download PDF Brochure @ https://www.marketsandmarkets.com/pdfdownloadNew.asp?id=15954762
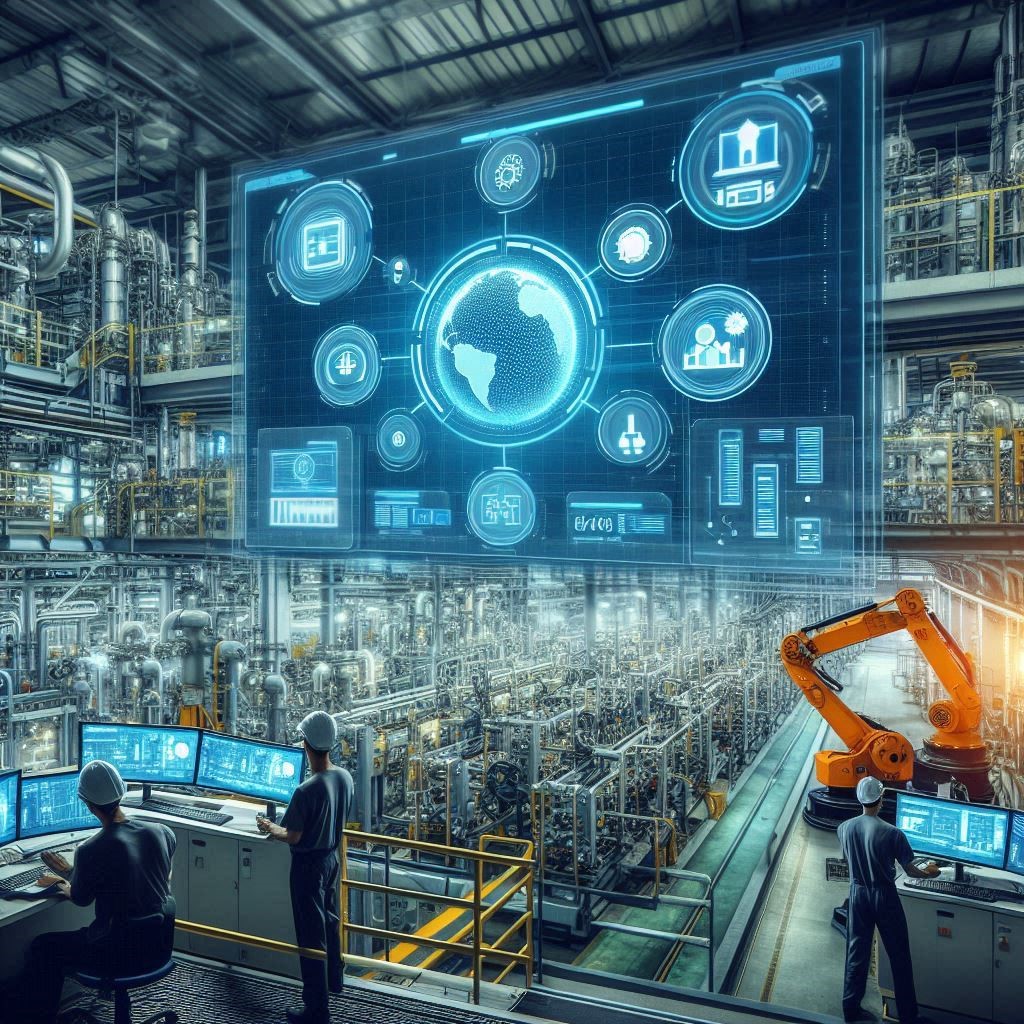
In sectors like oil & gas, aerospace, and energy, where downtime can lead to millions in losses, AI-enabled predictive FDC provides a critical competitive edge.
Cross-Platform Integration and Scalable Deployment
Another key benefit of AI in the FDC industry is its scalability and cross-system integration. AI models can be trained once and deployed across multiple production sites, machines, or product lines with minimal customization. Thanks to cloud and edge architectures, these solutions can operate across distributed environments with centralized control or localized decision-making.
AI-based FDC platforms can also integrate with other enterprise systems such as MES (Manufacturing Execution Systems), ERP (Enterprise Resource Planning), and digital twin platforms. This holistic integration enables context-aware fault detection that considers not only equipment data but also supply chain variability, operator behavior, and environmental conditions.
Addressing Challenges: Data Quality, Model Transparency & Cybersecurity
Despite its advantages, the implementation of AI in FDC comes with challenges. High-quality, labeled data is essential for training accurate models, but such data is often difficult to obtain in complex industrial settings. Moreover, some AI models, especially deep learning systems, act as “black boxes”—making it difficult for operators to understand the reasoning behind fault classifications.
To address these concerns, companies are investing in explainable AI (XAI) frameworks and combining AI with traditional rule-based methods for better transparency. Additionally, cybersecurity remains a key priority as AI models often access sensitive equipment and operational data. Secure data pipelines, access controls, and model governance are becoming standard practices.
Future Outlook: Autonomous Fault Management and Continuous Learning
The future of FDC lies in autonomous fault management systems that not only detect and classify faults but also take corrective action automatically—adjusting process parameters, rerouting workflows, or scheduling repairs in real time. AI will also play a role in continuous learning systems, where fault models evolve with every new data point or equipment upgrade.
As industrial operations grow more complex and interdependent, the combination of AI and FDC will be central to achieving zero-defect manufacturing, maximizing uptime, and enabling lights-out factories that require minimal human oversight.
Conclusion: Smarter Fault Detection for Smarter Industries
Artificial Intelligence is revolutionizing the fault detection and classification industry by delivering faster, more accurate, and predictive insights into industrial operations. Whether it’s improving process reliability, reducing downtime, or enabling proactive maintenance, AI-driven FDC is becoming a foundational capability for Industry 4.0 and smart manufacturing.
For organizations aiming to stay competitive, adopting AI-enhanced FDC systems isn’t just an upgrade—it’s a strategic shift toward a more resilient, adaptive, and efficient operational future.