The manufacturing sector is rapidly evolving under the influence of Industry 4.0, a revolution characterized by smart, interconnected, and highly automated factories. At the heart of this transformation lies human-robot collaboration (HRC), a concept where humans and robots work side by side, combining their respective strengths to enhance productivity, safety, and flexibility. Unlike traditional robotic systems that operate in isolation, HRC enables shared workspaces where robots assist humans with complex or repetitive tasks while humans bring creativity, problem-solving, and adaptability. This symbiotic relationship is increasingly becoming the cornerstone of smart factories, ushering in a new era of manufacturing excellence.
Defining Human-Robot Collaboration
Human-robot collaboration involves close physical and cognitive interaction between humans and robotic systems within a shared workspace. The idea is to leverage the complementary capabilities of both parties: robots provide strength, speed, and precision, while humans contribute creativity, intuition, and dexterity. Collaborative robots, commonly called cobots, are equipped with advanced sensors, force feedback mechanisms, and AI algorithms that allow them to sense human presence, respond safely, and adapt their behavior in real time. This fundamental shift from isolated robotic cells to interactive and responsive systems enables new workflows that were previously impossible or too risky.
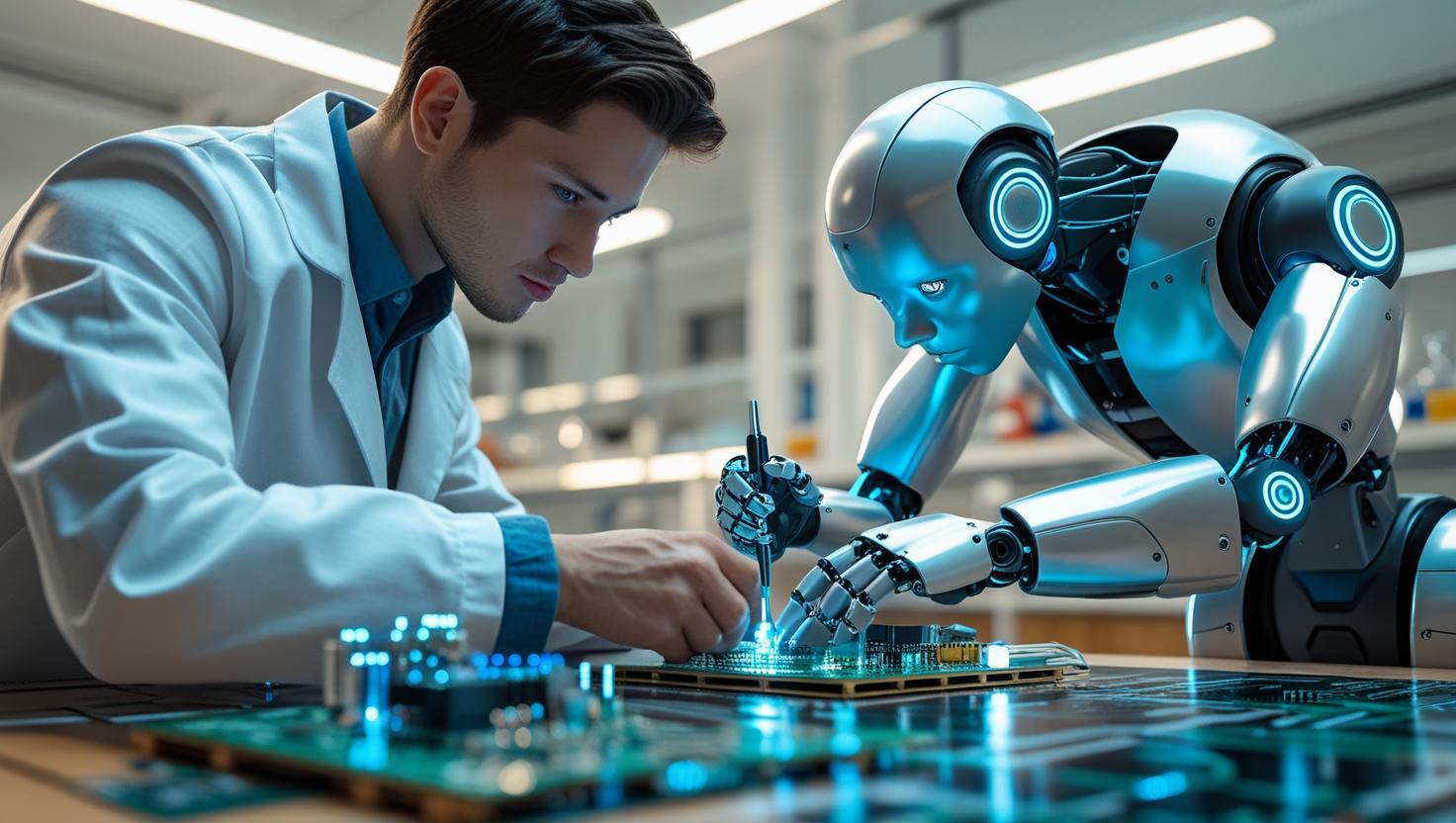
The Role of HRC in Smart Factories
Smart factories are digital ecosystems where machines, humans, and systems are interconnected through the Internet of Things (IoT), enabling real-time data exchange and automation. In these environments, HRC acts as a critical enabler of agility and efficiency. By integrating cobots alongside human operators, factories can optimize task allocation based on each partner’s strengths. Robots typically undertake monotonous, repetitive, or hazardous tasks, reducing human fatigue and injury risk. Meanwhile, human workers focus on oversight, quality control, troubleshooting, and tasks requiring fine motor skills or creative decision-making.
This synergy increases throughput and quality while providing the flexibility to rapidly shift production lines based on market demand. Furthermore, the continuous data flow from sensors embedded in cobots and surrounding systems allows for predictive maintenance and process optimization, key features of smart manufacturing. Consequently, human-robot collaboration not only boosts productivity but also enhances overall operational intelligence.
Technologies Enabling Effective Collaboration
The advances driving HRC are deeply rooted in emerging technologies such as artificial intelligence, robotics, sensing, and connectivity. AI enables robots to learn from human movements and adapt their assistance dynamically. Machine learning algorithms process vast amounts of sensor data, recognizing patterns that help robots anticipate human needs or avoid collisions.
Robotic arms with force sensors and compliant joints provide safe physical interaction by regulating the force applied, ensuring the robot yields when meeting unexpected resistance. High-resolution cameras and proximity sensors grant robots situational awareness, enabling them to detect human presence and environmental changes instantly.
Connectivity through IoT platforms facilitates seamless communication among robots, human operators, and factory systems. This interconnection ensures synchronized workflows and real-time response to deviations. Additionally, augmented reality (AR) tools provide humans with contextual information and guidance during collaboration, improving accuracy and reducing training time.
Download PDF Brochure @ https://www.marketsandmarkets.com/pdfdownloadNew.asp?id=194541294
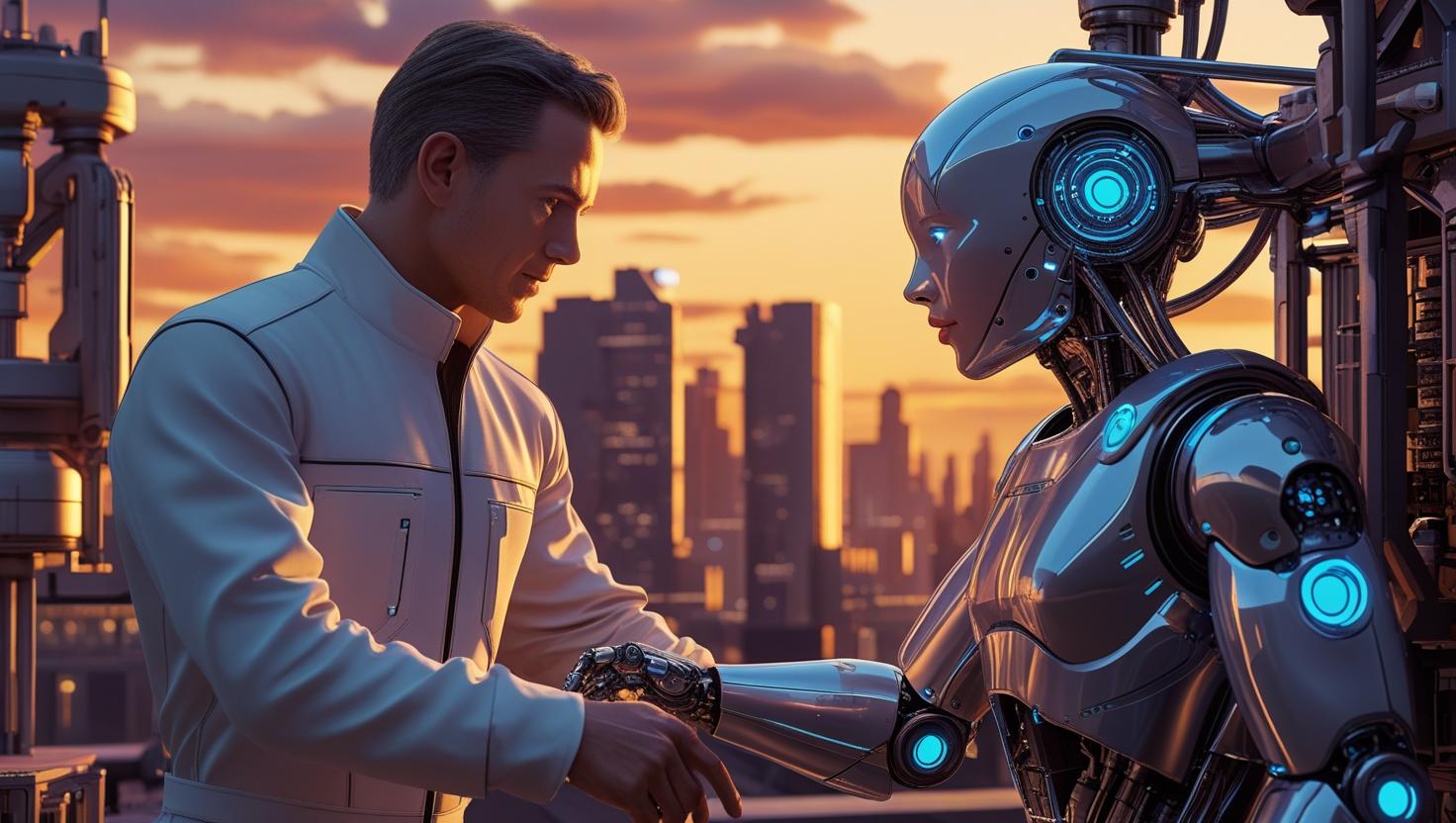
Practical Applications in Manufacturing
In assembly operations, human-robot collaboration is transforming workflows. Robots can perform repetitive actions such as screwing, welding, or picking and placing components with consistent precision, while humans oversee complex assembly stages, make real-time adjustments, and conduct quality inspections. This division of labor enhances both speed and accuracy.
Material handling is another domain where cobots shine. Robots assist workers by carrying heavy or bulky items, reducing ergonomic strain and injury risks. This is particularly valuable in industries like automotive or aerospace, where large components need precise maneuvering.
Machine tending is often automated using cobots to load and unload parts into CNC machines or presses. Humans monitor the machines and intervene when issues arise, creating an efficient partnership that maximizes machine uptime.
In quality control, robots equipped with vision systems scan products for defects or inconsistencies and flag anomalies for human review. This combination of robotic speed and human judgment elevates product reliability.
Maintenance processes also benefit from HRC, with robots assisting technicians by holding tools, providing diagnostics, or even executing remote repair tasks in hazardous environments.
Benefits to Manufacturers and Workers
The benefits of human-robot collaboration extend across multiple dimensions. For manufacturers, increased productivity, improved product quality, and reduced downtime translate directly into higher profitability. Cobots’ flexibility allows factories to adapt quickly to changing production requirements, fostering innovation and responsiveness to market trends.
Workplace safety is markedly enhanced as robots take over dangerous or physically taxing tasks. This leads to fewer injuries and associated costs, as well as a healthier workforce.
Employees benefit from reduced monotony and physical stress, improving job satisfaction and engagement. By offloading repetitive tasks, workers can focus on more creative, supervisory, and decision-making roles that demand human intellect.
From a cost perspective, while initial investments in collaborative robotics and AI may be significant, the long-term gains in efficiency, quality, and safety often yield substantial return on investment.
Challenges in Adopting Human-Robot Collaboration
Despite the clear advantages, integrating HRC into manufacturing processes presents challenges. The technical complexity of designing safe, responsive robots that can work closely with humans requires sophisticated hardware and software, which can be costly and time-consuming to develop.
Ensuring safety is paramount. Cobots must comply with strict international standards to operate alongside humans without risk. This involves extensive testing and certification, as well as continuous monitoring during operation.
The human factor also plays a critical role. Workers need adequate training to operate alongside robots and trust their reliability. Resistance to change and fear of job displacement may hinder adoption unless management fosters a collaborative culture emphasizing enhancement rather than replacement.
Additionally, cybersecurity is a growing concern, as increased connectivity in smart factories creates potential vulnerabilities that must be addressed through robust security protocols.
The Future Outlook for HRC in Smart Factories
Looking ahead, human-robot collaboration will become even more sophisticated and widespread. Advances in AI will enable robots to interpret more complex human cues, including verbal commands, gestures, and emotional states, making interactions more intuitive.
Robots will increasingly incorporate self-learning capabilities, allowing them to adapt autonomously to new tasks and environments without extensive reprogramming.
The integration of virtual and augmented reality will enhance collaboration further by providing workers with immersive guidance and real-time feedback, reducing errors and training times.
Moreover, as cobots become more affordable and user-friendly, small and medium-sized enterprises (SMEs) will adopt HRC, democratizing access to smart factory benefits.
In the broader manufacturing ecosystem, human-robot teams will connect seamlessly with supply chains and enterprise resource planning systems, creating fully integrated, adaptive production networks.
Human-robot collaboration represents a pivotal shift in manufacturing philosophy. By blending the strengths of humans and robots, smart factories become more agile, efficient, and safe. While challenges remain, ongoing technological advancements and cultural shifts promise a future where human-robot teams drive innovation and competitiveness.
The journey toward fully realized human-robot collaboration is not just about technology but about reimagining work itself—enabling humans to leverage their unique talents alongside intelligent machines in ways that enhance productivity, quality, and job satisfaction. Smart factories powered by this collaboration are set to become the engines of the next industrial revolution.
FAQ: Human-Robot Collaboration in Smart Factories
What is human-robot collaboration (HRC)?
Human-robot collaboration refers to the direct interaction and cooperation between humans and robots working together in a shared workspace. Unlike traditional robots that operate independently, collaborative robots (cobots) work alongside humans to complement their skills by taking on repetitive, dangerous, or physically demanding tasks.
How does HRC differ from traditional industrial automation?
Traditional industrial robots usually work in isolated cells separated from human workers to ensure safety. HRC involves robots designed with advanced sensors and safety features that allow them to work safely in close proximity with humans, enabling more flexible, interactive, and efficient workflows.
What benefits does human-robot collaboration bring to smart factories?
HRC enhances productivity by optimizing task allocation between humans and robots. Robots take on repetitive or hazardous tasks, improving workplace safety and reducing fatigue. Humans focus on tasks requiring creativity, problem-solving, and oversight. This collaboration increases flexibility, improves product quality, and supports rapid adaptation to changing production demands.
What technologies enable effective human-robot collaboration?
Key enabling technologies include artificial intelligence (AI), advanced sensors (vision, tactile, proximity), force-controlled robotic arms, Internet of Things (IoT) connectivity, and augmented reality (AR). These technologies allow robots to sense and respond to human actions safely and intuitively.