In an era where precision and speed are paramount, 3D metrology has emerged as a game-changer in the world of manufacturing. As industries race to meet the demands of high-performance products, tighter tolerances, and digital workflows, 3D metrology is revolutionizing quality assurance (QA) by providing faster, more accurate, and highly automated methods of measurement and inspection.
From aerospace to automotive, and from medical devices to consumer electronics, manufacturers are increasingly turning to 3D metrology technologies to improve product quality, reduce rework, and streamline production processes.
What Is 3D Metrology?
3D metrology is the science of measuring the physical geometrical characteristics of an object in three dimensions. It employs advanced technologies such as coordinate measuring machines (CMMs), laser scanners, structured light systems, and optical sensors to capture detailed, high-resolution data about a product’s shape, size, and surface.
These digital measurement tools provide a full 3D representation of an object, enabling manufacturers to compare real-world parts with their digital CAD models to detect deviations, misalignments, and defects at micron-level accuracy.
Why 3D Metrology Matters in Quality Assurance
Traditional quality control methods rely heavily on manual inspection, 2D gauges, and sampling—which are time-consuming, prone to human error, and insufficient for today’s high-complexity components. By contrast, 3D metrology enables non-contact, full-field measurements that are fast, repeatable, and far more accurate.
1. Speed and Automation
3D metrology drastically reduces inspection times. Where manual measurements might take hours, a 3D scanner can complete a full inspection in minutes. With the integration of robotics and automated metrology systems, inspections can be performed in-line or near-line without stopping production, ensuring real-time feedback and process control.
2. Enhanced Accuracy and Repeatability
Accuracy is critical in industries like aerospace and medical devices. 3D metrology tools deliver measurements within microns, offering detailed reports and analytics that allow engineers to trace defects, identify root causes, and correct them early in the production cycle.
3. Comprehensive Digital Records
With every scan, manufacturers generate a digital twin—a precise, 3D replica of the physical part. This digital record allows for ongoing quality tracking, reverse engineering, and better design iteration. It also supports traceability and compliance, which are essential in regulated sectors.
Download PDF Brochure @ https://www.marketsandmarkets.com/pdfdownloadNew.asp?id=203080758
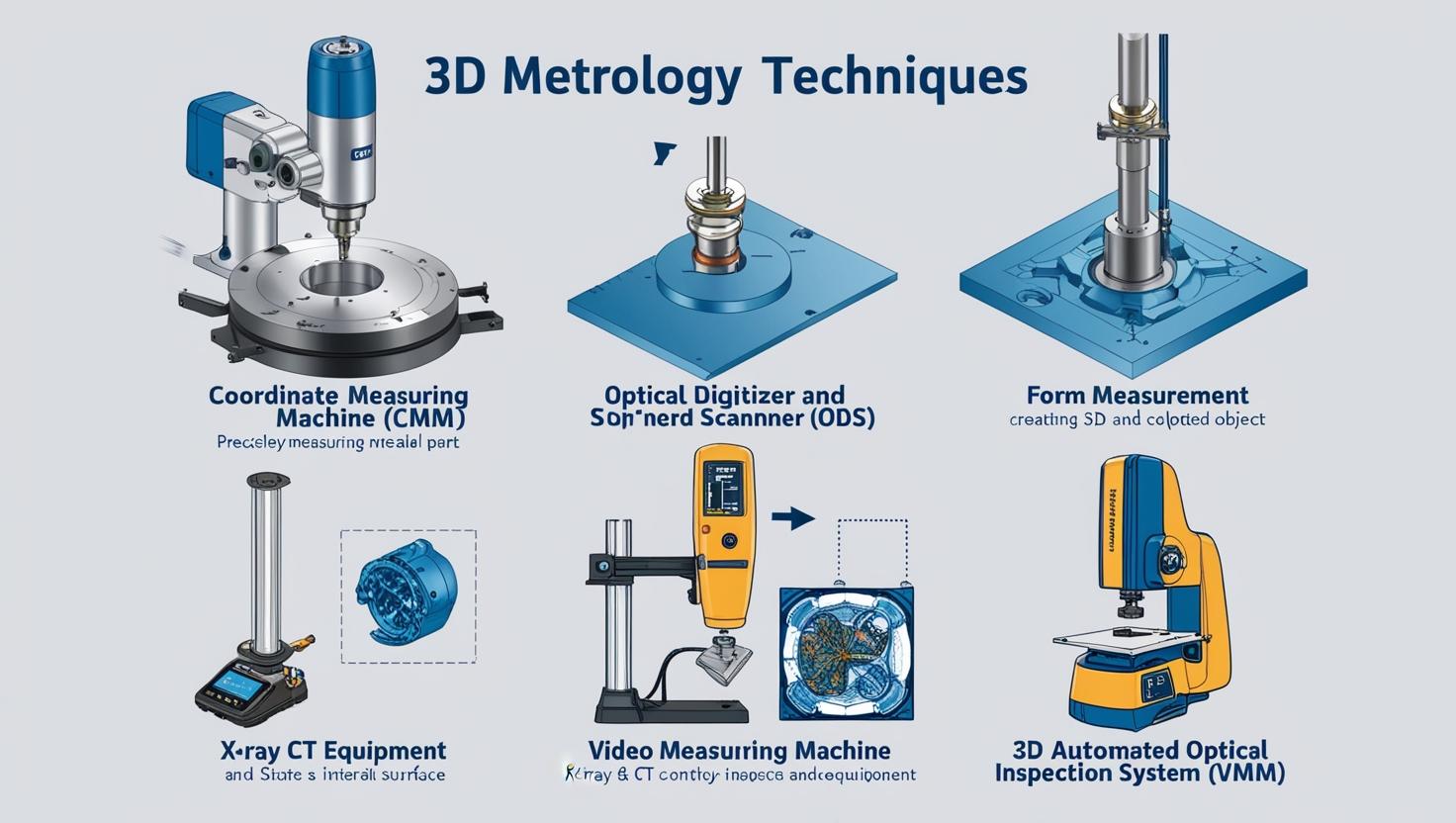
4. Improved Product Design and Development
During prototyping and product development, 3D metrology provides immediate insights into whether parts are within spec, enabling faster design validation and optimization. Engineers can use the data to refine CAD models, minimize tolerance stack-ups, and accelerate time-to-market.
Applications Across Industries
Automotive
In automotive manufacturing, 3D metrology is used to inspect body panels, align structural components, and monitor wear in injection molds. It ensures fit and finish consistency, critical for both safety and customer satisfaction.
Aerospace
Aircraft components require extremely tight tolerances. 3D metrology helps aerospace firms maintain geometric accuracy in turbine blades, fuselage assemblies, and composite materials, enhancing flight safety and reducing costly errors.
Medical Devices
Implants, surgical tools, and diagnostic machines demand perfection. 3D metrology enables high-precision inspection of small, complex shapes and supports documentation for regulatory compliance.
Tooling and Injection Molding
3D scanning allows manufacturers to monitor mold wear and validate tool performance. It minimizes scrap and ensures that produced parts consistently meet design specifications.
The Role of Software and AI in 3D Metrology
Modern 3D metrology systems are increasingly powered by AI and advanced software platforms that automate decision-making, flag deviations, and generate actionable reports. Machine learning algorithms can detect patterns in inspection data, helping to predict failure points and optimize manufacturing processes over time.
Integration with PLM (Product Lifecycle Management) and MES (Manufacturing Execution Systems) also enables seamless data flow between quality control and production, fostering a more intelligent, closed-loop manufacturing environment.
Future Outlook: Toward Fully Digital Quality Assurance
As manufacturers continue embracing Industry 4.0 and smart factory models, 3D metrology will become even more integral to quality assurance. The next wave of innovation includes:
-
Cloud-based metrology data analytics
-
Edge computing for in-line quality checks
-
Wireless, handheld 3D scanning devices
-
Greater integration with digital twins and simulation tools
These advancements will allow manufacturers to not only identify defects but also to predict and prevent them, turning quality control into a proactive, predictive process.
3D metrology is not just improving how manufacturers measure parts—it’s redefining how they approach quality assurance at every stage of the production lifecycle. By enabling faster inspections, reducing errors, and enhancing data-driven decision-making, it supports a shift toward smarter, leaner, and more competitive manufacturing operations.
FAQs: 3D Metrology and Quality Assurance in Manufacturing
1. What is 3D metrology?
3D metrology is the process of measuring the three-dimensional physical characteristics of an object using advanced technologies like coordinate measuring machines (CMM), laser scanners, and optical sensors to capture precise geometric data.
2. How does 3D metrology improve quality assurance?
It enables faster, more accurate, and comprehensive inspections by providing detailed 3D measurements that detect deviations from design specifications, reducing errors and rework in manufacturing.
3. What industries benefit most from 3D metrology?
Key industries include automotive, aerospace, healthcare (medical devices), consumer electronics, and tooling/injection molding where precision and quality are critical.
4. Can 3D metrology be integrated into automated production lines?
Yes, with robotic integration and advanced software, 3D metrology systems can perform in-line or near-line inspections, delivering real-time quality feedback without halting production.